- インダストリー4.0とは
- インダストリー4.0へと繋がる産業革命の歴史
- インダストリー4.0の本質
- これまでのIT活用とインダストリー4.0の違い
- インダストリー4.0をどう進めるのか
- インダストリー4.0で進む連携とプラットフォーム
- 技術・組織・システム・人材の連携が重要
インダストリー4.0とは
インダストリー4.0は、2011年にドイツが提唱した製造業の長期ビジョンである。日本では第四次産業革命とも呼ばれる。
インダストリー4.0とはいったい何なのか
インダストリー4.0は、ドイツ政府が主導し、産官学共同で進めている国家プロジェクトです。人類史上4回目の産業革命、つまり「第4次産業革命」を起こす取り組みとしており、そのコンセプトは「スマートファクトリー」(考える工場)です。
– ビジネス+IT
今さら聞けない「インダストリー4.0」の基本、IoT で何が変わるのか
インダストリー4.0へと繋がる産業革命の歴史
第一次産業革命
歴史を振り返ると、第一次産業革命は、1785年ジェームス・ワットの蒸気機関の発明に始まったとされる。これまで人力や馬力、風車・水車で行っていた作業を、蒸気の力を利用して機械化を進めたもので動力の革命とも呼ばれる。
第二次産業革命
第二次産業革命は、1865年頃からイギリス、ドイツ、アメリカを中心に始まったもので、重工業の技術革新、電気の利用、大量生産を実現した。1908年から開始されたフォードのT型製造では、ベルトコンベア方式を導入して、ひとつの製品を大量に生み出す大量生産方式の基本形が完成した。
第三次産業革命
それに続く第三次産業革命は、ソフトウェアを用いた自動化の革命と位置付けられる。その走りが、1969年に発表された世界で最初のPLC(プログラマブル・ロジック・コンピュータ)のModicon 084だ。
PLCはそれまでのリレー制御盤(物理的に電気信号を入り切りして制御)に代わり、プログラム可能なソフトウェアとして生産設備の制御を実現した画期的な発明だった。
PLCも発表当初は、これまで生産現場に大量に導入されていたリレー制御盤と同じ機能を、1つのボックスが持ちうるということがなかなかユーザーに理解されず、広く製造現場に受け入れられるようなったのは1970年代半ばになってからだった。
インダストリー4.0の本質
現在はまさに第三次産業革命の最終段階であり、次のビジョンがインダストリー4.0といえる。
インダストリー4.0の本質は、製造業のデジタル化である。そもそもなぜドイツでインダストリー4.0というビジョンが作られたのか。それは、製造立国であるドイツの焦りからだといえる。
GDPに占める製造業の割合が約22%と大きなドイツでは、大企業だけでなく中堅中小企業に至るまで、国としての製造業全体の競争力を維持し、国内でものづくりを続けることが重要であった。
世界を見ると、ITを武器に新たなビジネスモデルを創出するアメリカと、比較的安価な労働力とレガシー設備を気にせず最新技術に投資できる中国を相手に、競争力を保ち続けるために何をするべきなのかが大きな課題だといえる。
その結論が、インダストリー4.0というビジョンであった。
製造業の競争力を維持・強化するには、これまで市場にない商品を競合に先駆けて、顧客の好みに合わせた形で、高い品質の元で、リーズナブルな価格で提供する、という視点が極めて重要になる。
これは製造業にとって新しいことは何もない。しかし、多様化する顧客の好みに合わせた製品を、従来の大量生産を前提としたコンセプトをベースで生産するには限界が来ている。それをデジタルの力を使って加速させ、製造業の競争力を強化するのがインダストリー4.0の目的である。
これまでのIT活用とインダストリー4.0の違い
では、これまでの製造業におけるITの活用とは一体何が違うのか。これまでも製造業では、設計のデジタル化(CADの導入)、センサーを駆使した生産状態の見える化など、様々な領域でデジタル化による効率化を実施してきた。
インダストリー4.0の本質は、従来の部分効率化にとどまらず、製造業の全バリューチェーンを通じたデジタル技術のフル活用にある。
プロセスごとにバラバラの専用システムで構成されていたデジタル化要素をプラットフォーム上でつなぎ、シームレスに製品設計から設備設計、製造までつなぐことが目標である。
そうすることで、例えば製品が設計されてから、必要な部品の情報も含めて自動的に製造ラインまで情報がつながり、5分後には製造開始できるというような世の中を目指している。
これを実現するには、設計データをそのまま製造側に渡せる状況までコンプリートすることに加えて、製造側も設備をモジュール化・標準化することが必須である。
設備のモジュール化とは、究極的には生産設備をプラグ&プレイでつなげられるように標準化していくイメージに近い。
現在、パソコンにUSBケーブルでプリンターをつなげば印刷できるということを疑う人はいない。しかし、15年前はパソコンとプリンターの相性というものが確かに存在して、それをつなぐためのコツや設定が必要であった。
現在の生産現場は、そのようなすり合わせの塊で、そこに日本企業の強みがあるともいえる。今後、製造業のデジタル化が進み、すり合わせ自体の付加価値が相対的に減っていく中で、日本企業は改めて自身の強みを明確にしていく必要があるだろう。
インダストリー4.0をどう進めるのか
今後、製造業のデジタル化はどのように進むのか。アメリカのオバマ大統領も視察し話題となった2016年4月のハノーバーメッセも踏まえて考察したい。
グローバルな連携
まず一点目は、グローバルでの連携強化である。時にインダストリー4.0は、ドイツ対アメリカ対日本のように国同士の対抗という目線で語られることがある。しかし、各国はそのような表面的な対抗ではなく、むしろ協業を模索している。
2016年4月28日に日独共同声明が締結された。これはIoTやインダストリー4.0に関する日独の連携強化を目指したもので、今後、日本の経済産業省とドイツ経済エネルギー省の間で局長級対話が毎年実施され、国レベルで進捗や成果を共有していくことになる。
これとは別に、民間レベルでドイツのPFI4.0(Platform Industrie 4.0)とGE等が主導するアメリカのIIC(Industrial Internet Consortium)とが標準化や共同プロジェクトで協力を強化することを発表した。
ドイツは他にも中国やフランスとも協力関係を強化しており、国の枠組みを超えた産学官の連携が加速していくだろう。
異業種間の連携
もう一点は、異業種間の連携である。今年のハノーバーメッセでは、SAPやIBMといったいわゆるIT系企業と製造業がコラボした展示も多くみられた。
製造データのビッグデータ解析やクラウド連携、基幹システムと製造系システムの連携など、これまである程度住み分けがされていた領域でも業種を超えた連携が進んでいくことは間違いない。
インダストリー4.0で進む連携とプラットフォーム
製造業のデジタル化に伴い、新しいビジネスも今後続々と誕生していく。例えば、工場同士のデータ連携が進めば、それを連携するプラットフォームが生まれる。
身近な例で飲食業界を見てみると、インターネット上でお店の宣伝をしたい時、これまでは自分でホームページを一から構築するしかなかった。大手チェーンや規模の大きな店舗であればそれも可能だが、小さな店舗ではそのような体力もノウハウもなかった。
しかし、ぐるなびや食べログのようなプラットフォームが出てきたため、そこに簡単なデータを入力するだけで、自社を宣伝できるようになった。
一方で、そのプラットフォームに乗らないと、お店の存在すら見つけてもらえずビジネスそのものが危うくなる事態にもなりかねない。
また、業種を超えた連携の結果、ビジネスプロセスのアウトソースも加速する。サイバーセキュリティ対策などは、自社で専任スタッフを置くことと、セキュリティの専門企業にオペレーション含めてすべてアウトソースすることを目的に応じて比較検討することになるだろう。
技術・組織・システム・人材の連携が重要
いくら大企業といえどもこのデジタル化のトレンドに対して、自社だけで全方位で立ち向かうことは不可能だ。繰り返しになるが、自社の強みと弱みの把握し、戦うところは戦うが、戦わなくてもいいところは標準品を使って戦わない、つまり競合領域と協業領域の明確化がより重要になる。
日本企業にとっては、デジタル化はもちろん脅威だけでなく機会もある。開発から製造までをつなぎフレキシブルな製造が可能になれば、これまで製造側の制約から難しかった細かな仕様変更も可能になる。
例えば市場が急拡大する新興市場向けに、1つの製造拠点から多様な国・文化に合わせたカスタマイズ製品を供給できれば、これは大きなビジネスチャンスになりうる。
今後も人工知能、3Dプリンター、ビッグデータなど様々なイノベーションが生まれるが、忘れてはならないのは、製造現場を含めた製造の全バリューチェーンに対して、自社の強みを最大限活用できるデジタルプラットフォームを構築し、それらのイノベーションをうまく取り込むことだ。
日本版インダストリー4.0の実現に向けて、技術のみならず組織、システム、人材育成含めて先進技術を真に「使い倒せる」体制作りが製造業にとっては急務となっている。
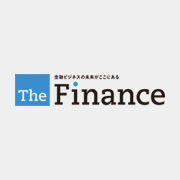
- 寄稿
-
シーメンス株式会社神澤 太郎 氏
デジタルファクトリー /
プロセス&ドライブ事業本部
ビジネスエクセレンスグループ
グループマネージャー