ものづくり現場のDXによる働き方変革
~リコー流のDX展開・実践メソッドと実践事例のご紹介~
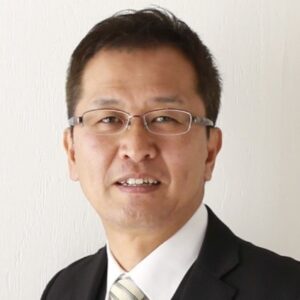
- 特別講演
-
【講演者】
- 株式会社リコー
- リコーデジタルプロダクツビジネスユニット
- 経営戦略本部 経営統括センター DX推進室 室長
森田 雅則 氏
<なぜ製造業のDXが進まないのか>
DXが製造業において進まない要因は、次の4つが考えられる。1つ目はどこから手を付ければよいのかわからない点だ。経営者から「DXが重要だ」と言われていても、現場は何から始めればいいのか分からない。2つ目は、どうしても工場間でバラつきがある点だ。DXはデータ連携によって力を発揮するために、業務プロセスのアウトプットであるデータが重要だ。業務プロセスや運用している仕組みがバラバラでは、データの連携が進まずDXも進まない。3つ目は、一足飛びに高いレベルを狙いがちな点だ。AIはデータがあって初めて成立するため、データがなければ使いこなせない。現場のデータを収集することから始めることが重要である。4つ目は、DX人材不足だ。そもそもITリテラシーの高い人材がいない、という声もよく聞かれる。日本のものづくりの現場は匠の意識が高く、経験と勘が評価されてきた点もDXの阻害要因の1つだ。
<デジタル(DX)は改善活動の手段>
「DXをやるぞ」という経営トップの宣言は、DXそのものが目的になっていることが多い。デジタル(DX)は、改善の手段であるとの認識が重要だ。よって改善文化の醸成がないところに、改善手段のデジタルを導入しても浸透は難しい。
かつては経験則や直感が重要視される、「ヒューリスティック」と呼ばれるアナログなものづくりの思想が中心であった。今後はデータドリブンで行うサイバー上のプロセスと、フィジカル上のプロセスの両輪で、連携あるいは使い分けをしながらものづくりを進めていくことが重要になる。現場・現物・現実を意味する三現主義は、現在では遠隔地でもカメラによって現地に行くのと同等の情報を得られるようになった。
リコーグループの生産拠点では、“安全、5S、KAIZEN”など生産のベースとなる「12の基礎」をRICOH Way Production System(RWP:生産のリコーウェイ)として体系的にまとめている。このRWPの浸透を通じて、生産基盤強化を実践し改善文化を醸成すると共に、それをデジタルによって加速し、そして変革に挑戦している。
<ものづくりDXビジョン>
DXの目的は、デジタルツインの活用により、ものづくりの現場とオフィスで“はたらく人”の生産性と働き方を変革することである。その手段が、デジタル技術の活用・データ分析だ。企業の体質強化および利益創出は当然のこと、快適で多様な働き方の実現がDX推進の狙いである。
<DX実践メソッド>
具体的には「One Company」、つまり個別最適から全体最適を目指す。従来は、各工場が独自にものづくりを進化させてきた結果、仕事のやり方も工場間で異なるケースが多い。そこで閉ざされた環境の中で個別に保有してきたデータを、オープンにして連携させ、バーチャル上では1つの会社を目指す。従来のように、オンプレミスでデータを保管していると、外部のサプライヤやお客様と連携するのは難しい。そこで弊社ではクラウドを活用し、グローバルな展開、連携の強化を進めている。
全体最適化を加速させるためには、Top DownとBottom Upの両輪の活動が必要だと考える。トップデザイヤと現場の課題を結び付け、デジタル化を加速し、真に効果が出る活動へと昇華させていく。デジタル化は大きな投資効果がすぐに出ない。効果がある程度出るところまで、我慢が必要になるという理解が重要だ。さらに現場の理解と実践も重要になることから、Top DownとBottom Upをつなげ、両輪をうまく司る組織の構造も必要になる。
<3つの展開・実践メソッド>
リコーのDX展開・実践メソッドの1つ目は、デジタル化する「活動領域」をフォーカスし、狙いを明確化することから始まる。2つ目は「データ管理標準化」を行い、データ連携のしやすい環境を作る。言い方を変えれば、データの共通化、民主化、共有化の仕組みを作ることだ。3つ目の「展開ステップ」は、『データ収集・可視化』、『分析・予測』、『制御・最適化』の順に、データ利活用レベルをアップさせていく。
<『ものづくり現場』における3つの展開・実践メソッド展開>
メソッド1の活動領域は、工場間における共通業務に絞った。工場拠点のユニークなオペレーションを統一化することは難しいため、共通業務をまず探し出したのである。共通業務からセンシングしたデータを収集・連携していく。これによって組織の壁をそれほど感じずに済むこととなる。リコーでは業務を13の領域に分類し、データセンシングの領域を決め、領域毎にDX対象となる業務を体系化している。
メソッド2のデータ管理標準化は、データ収集・蓄積・活用に至る一連のデータマネジメントを標準化し、全工場へ展開している。まずデータを取り、「共通化」するためのデバイス開発を行った。データを貯めるところはデータの「民主化」と呼び、共通データプラットフォームを作り込んだ。データーアクセスナビゲーションなど、データの活用は「共有化」と呼ぶ。
メソッド3の展開ステップは、データの可視化がLv1と考える。Lv2では、データをどう分析・予測するかを決め、分析・学習・将来予測のためのモデルを作る。Lv3では、AIを使うなどして蓄積したデータの最適な判断・実行を行う。これらのステップの順序を守りながら、展開していくことが重要になる。当社では2018年からLv1に取り組み、その後はLv2、Lv3を順次取り入れ、並行的・継続的に現在も行っている。Lv1で効率化による効果の創出、Lv2で効果拡大、Lv3で効果最大化を見込めるほか、Lv3になると快適な働き方へと大きく変わってくると考える。
Lv1の事例は、ダッシュボードを共通化しデータのモニタリングによる改善の加速や、それぞれの領域をデジタルによってリアルに再現できるデジタルツインの活用が挙げられる。Lv2の事例は、作業指示通りに手が動いているかをセンシング・モニタリングすることによる品質の作り込みだ。トラブル管理履歴データ分析においては、スマホを活用している。場内のWiFiを介して、クラウドにデータが上がる仕組みだ。Lv3の事例となるMFPユニットの接着剤塗布工程においては、リアルタイム品質予測や自動制御によって人手による確認と調整作業を100%削減した。
<『オフィスワーク』における3つの展開・実践メソッド展開>
柔軟な働き方を促進するために、ITインフラを刷新し、時間と場所を選べる働き方を実現している。2017年には、グループ内の基盤ITツールとしてMicrosoft 365の展開を開始した。2018年には、グローバル約11万人のコミュニケーション基盤をMicrosoft 365に切り替え、コロナ禍を経て全従業員のITリテラシーが向上している。さらに柔軟な働き方を加速させるために、オフィスワークの3M「面倒」「マンネリ」「ミスできない」というストレスを、デジタル技術でオフィスワークから取り除くことを目指す。
メソッド1の活動領域は、ローコードアプリによる業務のデジタル化領域に絞った。業務部門自らが導入できる領域を対象とし、自分の業務は自分で改善するという全員参加型の活動である。ローコードアプリを組合せたシステムを汎用パッケージ化し、類似業務に展開していった。メソッド2のデータ管理標準化は、ローコードアプリの標準化である。情報の入力から分析まで、一気通貫でローコードアプリを組合せてシステムを汎用化した。メソッド3の展開ステップは、Lv1の業務のデジタル化、Lv2の情報・データの蓄積、Lv3のAI活用(分析自動化)を、働き方の変革と連携させながら実現していく。
事例は、グローバルで数百件にのぼるデジタル化テーマの統合管理だ。テーマも管理ツールを使いこなしながら、現場が重複した活用にならないよう、オペレーションが簡素化・ペーパーレスになるようにデータをまとめている。